Sensor-Actor-Controller units (SAC units)
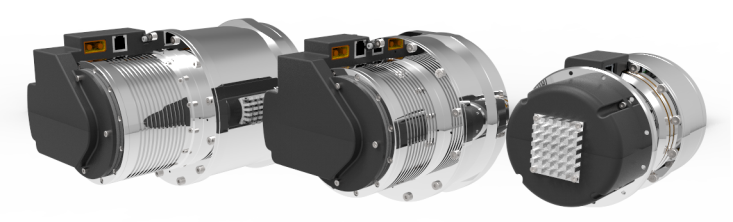
Our highly integrated sensor-actuator-controller units (SAC units) for robotic joints address the increasing need for easy to use components in the design of modern high-performance robotic systems. Following strict design principles and an electro-mechanical co-design from the beginning on, our development resulted in highly integrated modules. Each SAC unit includes a motor, a gear unit, an IMU, sensors for torque, position and temperature as well as all necessary embedded electronics for control and communication over a high-speed EtherCAT bus. Key design considerations were easy to use interfaces and a robust cabling system. Using slip rings to electrically connect the input and output side, the units allow continuous rotation even when chained along a robotic arm.
In order o realize a dual arm system for ARMAR-6 with a payload of 10 kg per arm, we followed an exoskeleton design approach that includes SAC units in three sizes: The first three shoulder joints are driven by large SAC units with a torque capacity of 176 Nm, the elbow and its two adjacent joints by medium sized SAC units with a torque capacity of 123 Nm and the wrists by small units providing 64 Nm of torque.
Universal Controller Module (UCoM)
For sensorimotor control the Universal Controller Module (UCoM) was developed, which is integrated seamlessly in our computer and software architecture. Different drivers for controlling e.g. brushed motors, brushless motors or valves can be connected to the modules as piggyback boards to control different types of actuators. With the 3way-brushdriver board each UCoM is able to control three brushed DC motors at 24V with up to 5A and can decode six quadrature coded encoder signals. The UCoM is equipped with a DSP and a FPGA, which processes data and equips the DSP with a large number of general purpose IOs. Special attention in design was given to a small size and low power consumption. Communication is done by CAN-Bus and various programs can be uploaded to configure each module to the needs of the specific actuators the module is assigned to.